Quality of Material used in Oil and Gas Industry
Industry standards for quality of materials have changed along with time. Iron has been switched for steel, the casting process has evolved, and so has forging. Carbon has altered the whole engineering field, in the matters of material strength and mass. Unlike steel and aluminium, one is strong but heavy while other is light but weak; carbon steel is strong and light.
Below is the overview of the current industry standards for quality of materials used to make elements of piping systems (which includes pipes, joints, valves, flanges, fittings and other accessories).
Elements and Alloy
Rust has been a cancer to all the major industries around the globe. Alloys have changed and saved all the major manufacturing industries. By simply adding a few percent of other metals one can give birth to a new material according to the given need.
As of now, Oil and Gas Industries’ have four standard materials for quality piping systems. These are:
- High-Temperature Carbon Steel
- Carbon Steel Alloy High-Temp
- Carbon Steel Alloy Low-Temp
- Austenitic Stainless Steel
Beyond iron, many elements have been tried and tested in the composition. It all gives the final alloy different strengths and weaknesses.
Most of the time, in the industry these materials are used:
Carbon, Manganese, phosphorus, sulphur, copper, nickel, chromium, molybdenum, and vanadium, to make different alloys.
High-Temperature Carbon Steel
Carbon steel is a steel alloy that contains carbon, anything ranging from 0.12% to 2%.
The term in itself is the definition. Though it is not carbon steel made in high-temperature rather it is carbon steel for high-temperature purposes. ASTM A106, A216, A234, and A105 are generally used in the industry to build the piping system.
ASTM A106 (Gr. A and B) are used for seamless carbon steel pipe for high-temperature service.
ASTM A216 (WCA, WBC, WCC) are used for carbon steel castings for valves, flanges, fittings, or other pressure-containing parts for high-temperature services.
A106 A is carbon and silicon, the tensile strength grade is 330 MPa. The ingredients of A106 B are carbon, manganese and silicon, the tensile strength grade is 415 MPa. The ingredients of A106 C are carbon, manganese and silicon components, the tensile strength grade is 485 MPa.
The quality is suitable for assembly with other castings or wrought steel parts by fusion welding. Besides A106 and A216, A234 and A105 are used to make fittings and other units.
Carbon Steel Alloy High-Temp
Carbon steel alloy is also known as Ferritic steels. Carbon steel alloy specifications are defined as low and intermediate-alloy steels containing up to and including 10 % chromium. This alloy is used for high temperatures as well. ASTM A335, A182, and A217 are used to build up the system.
ASTM A335 (Gr. P1 to P92) are used to make seamless pipes for high-temperature services.
ASTM A217 is generally used for steel castings, martensitic stainless steel and alloys steel castings for valves, flanges, fittings, and other pressure-containing parts. Again, intended primarily for high-temperature and corrosive service.
ASTM A335 (ASME SA335) P11 Grade Pipes have, Chrome content at 1.00% to 1.50%, Moly content at 0.44% to 0.65%, Minimum tensile strength is 415MPa, and minimum yield strength is at 205 Mpa.
Carbon Steel Alloy Low-Temp
Low-temperature carbon steels have been developed mainly for use in low-temperature equipment. And especially for welded pressure vessels. They are low to medium-carbon (0.20 to 0.30%), high-manganese (0.70 to 1.60%), silicon (0.15 to 0.60%) steels, which have a fine-grain structure with uniform carbide dispersion.
Carbon Steel Alloy Low-Temp is a Nickel based alloy steel plate especially used for low temperature applications below – 150° F. Mainly used in low temperature applications in chemical plants below -50° C. ASTM A333, A420, A350, and A352 are used to build up the system.
ASTM A333 Grade 6 pipe is common use material for low temperature services in above -45℃, with yield strength minimum at 240 Mpa, and tensile strength 415 Mpa.
Other Carbon steel alloy low-temp includes: A420, A350, A352; which are used more in fittings, valves and flanges.
Austenitic Stainless Steel
Austenitic stainless steel is known for its durability, strength, and corrosion resistance. Among the others, it is easy to produce and less harmful to the environment.
Austenitic stainless steel contains 8 to 12 percent nickel, as well as nitrogen, carbon, and many other elements in solution. Chromium is what gives the steel its high corrosion resistance, while nitrogen acts as a stiffening agent.
Austenitic gets its name from Austenite. Austenite is a crystalline structure, with face-centred-cubic lattice structure. Which is present throughout both hot and cold temperatures. Nickel, Magnesium, and Nitrogen are stabilising elements for the austenite structure. ASTM A312, A403, and A182 are used to build up the systems.
0 A312 (TP 304, 316, 321, 347, etc) are used for seamless, straight-seam welded, and cold worked welded austenitic stainless steel pipes, intended for high-temperature and general corrosive service. In general the tensile strength of this pipe is minimum at 480 Mpa.
A403, A182 are other Austenitic steel, which are used to make fittings, valves and flanges.
The materials mentioned above are not singular in themselves. Quality varies with change in composition. All materials have grades which change their cost and qualities.
While Austenitic steel is the most used metal in manufacturing, other carbon steels are reaching varied parts. High-temperature carbon steel is expensive and provides better quality for high-temperature fluid. On the other hand, austenitic steel is famous for its anti-corrosion elements. So it is not limited to the Oil and Gas Industry.
These four materials are crafted for different types of functions. The use of all four of those are common in the oil and gas industry. As the requirements will improve, so will the materials.
Related News
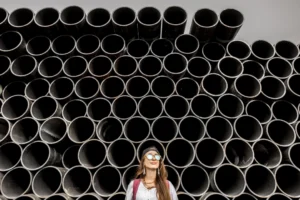
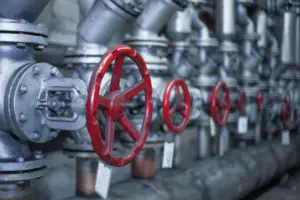

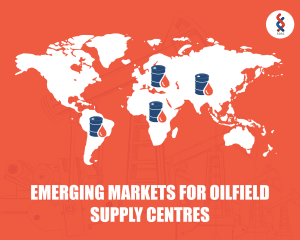
Emerging Markets for Oilfield Supply Centres
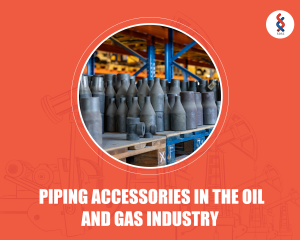
Piping Accessories in the Oil and Gas Industry
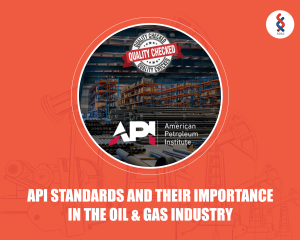